4 min read
Pioneering Complex Castings From Concept to Production
By: Alex Grainger on Jul 10, 2024 11:00:41 AM
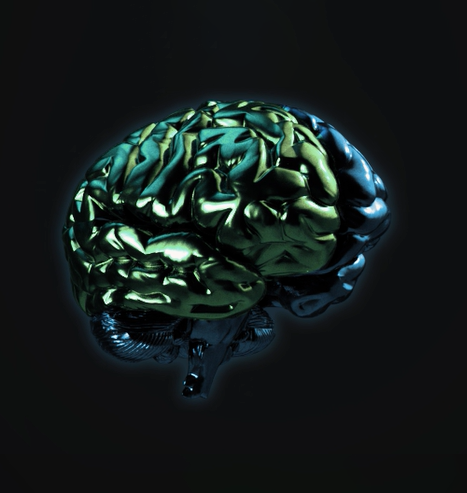
As a world-leading brand in the business of engineering complex, high-integrity casting and machining solutions, our mission is always to keep the world moving forward.
Our specialist expertise has evolved over the years, as we’ve transitioned from a heritage tool shop to a global hub for cutting-edge aluminium casting. Now, we have the facilities, knowledge and innovative mindset to support our clients with a fully integrated process from initial design concepts right through to fully machined parts.
In this article, we’ll uncover the rules of good design when it comes to complex castings and how we’re uncovering new and inventive opportunities for product optimisation.
We’ll also deep dive into our process to help you understand how we craft expertly engineered solutions with some of the industry’s most rapid lead times.
Three Requirements for State-of-the-Art Casting Design
1. World-Leading Facilities to Drive Innovation
Casting and machine engineering best practices are constantly in flux, requiring significant regular investment into the latest machinery, technology and facilities to support the most groundbreaking advancements of the next generation.
We are constantly expanding our facilities to support the creation of the most innovative, high-integrity, complex and lightweight metal structures of today.
This includes dedicated virtual engineering and design offices, four foundries, two machine facilities, two metrology centres, in-house 3D sand printing, two heat treatment facilities, a setting centre, and three NDT PDI facilities.
2. Material Development for Highly Optimised Results
One of the most crucial aspects of casting design is the product optimisation process, one that often gets overlooked in favour of speeding up lead times. But when it comes to next-generation castings and metal, you need streamlined material developments to optimise for weight, strength and energy absorbancy, without compromising on cost, time and resources. This ensures you’re building the leanest and most efficient product on the market.
Our product engineers and technicians work to drive efficiencies into the process. We can also service the production tooling in our tool shop. For materials development, our in-house heat treatment facility, laboratory and independent on-site test house allow us to refine our current alloys by continuously analysing the results.
3. Big Data in Virtual Engineering
At its highest level, engineering is a numbers game – one that we have a deep knowledge and understanding of. Virtual engineering, AI, digitalisation and simulation are some of the future-led technologies that allow us to extensively test prototypes and the most complex metal parts in a vast range of virtual environments, ensuring the highest integrity precision castings made right the first time.
Using controlled processes and computerised imaging in our digital factory, we can reduce the risk of defects during the solidification process for an exceptionally fine-tuned result.
One Streamlined Process
Our goal is always to get your innovative ideas to market fast, which is why we work collaboratively alongside your engineering team to provide the specific support you need. Taking full ownership of the project, we can achieve lightning-fast lead times by expediting any of the below processes.
Conceive
Nearly all of the world’s most complex castings started with an idea. Whether you already have one or need help coming up with a unique casting solution to solve your complex engineering problems, we are driven to help you meet even the most demanding requirements.
The process always starts with a complimentary project review, where our lead engineers will review your ideas or engineering pain points and devise a plan to realise and optimise your metal parts.
Simulate
Cutting-edge simulation software lets us test and optimise your product so that we can make it right the first time, saving valuable time, money and wasted resources creating multiple prototypes.
Produce
From crafting leading-edge prototypes at the forefront of sustainable engineering to ultra-high-performance alloys for the motorsports industry, our production capabilities are built on a ground-up fundamental understanding of the translation of liquid metal to a finished product.
Sand reclamation and reprocessing of our metal both help reduce waste but also allow us to control the inputs to the process.
Validate
Our fully integrated Design for Manufacture (DFM) process includes tailored validation strategies to mitigate casting risks and deliver quicker than ever before.
This includes material analysis spectrometers to enable traceability of process variables and chemical and compositional analysis, computer tomography and digital radiography for integrity assurance, and GOM (Geometric Optical Measurement) scanning to map external profiles and produce a 3D CAD model. We also provide in-house leak testing and tensile testing for ultimate quality assurance.
This is all part of our seamless New Product Introduction process which aims to deliver best-in-class engineering, drawing on diverse industry expertise tailored to the needs of the environment.
What We Can Offer
A Fully Integrated, Scaleable Service
From one-off prototypes to high-performance niche series volumes, our capabilities draw on decades of knowledge to adapt flexibly to your needs.
Cutting-Edge Prototyping and Virtual Engineering
We use the latest simulation software and technology to accelerate the optimisation process without compromising on product and resource efficiency.
Rapid Lead Times and Refined Results
As one of the world’s most exceptional metal foundries, we offer some of the most cutting-edge rapid technologies to enhance and accelerate innovation, with a focus on streamlining NPIs to help you stay one step ahead of your competition.
What's next...
Want to learn more about our process, and capabilities, or simply chat through your ideas with one of our lead engineers? Feel free to get in touch.
Related Posts
EV components: Surviving the valley of death with sand casting
When it comes to producing components for electric vehicles that are lighter (creating lighter,...
GRAINGER & WORRALL CONFIRMED AS ASTON MARTIN DB11 ENGINE CASTINGS PARTNER
Aston Martin has confirmed Grainger & Worrall (GW) as its preferred engine castings partner for the...
Hydrogen Combustion Engines: What are the opportunities and challenges?
In this article, we’ll take a look at the opportunities and challenges of using hydrogen converted...