4 min read
Driving Sustainability With State-of-the-Art Virtual Engineering
By: Alex Grainger on Jul 29, 2024 5:05:10 PM
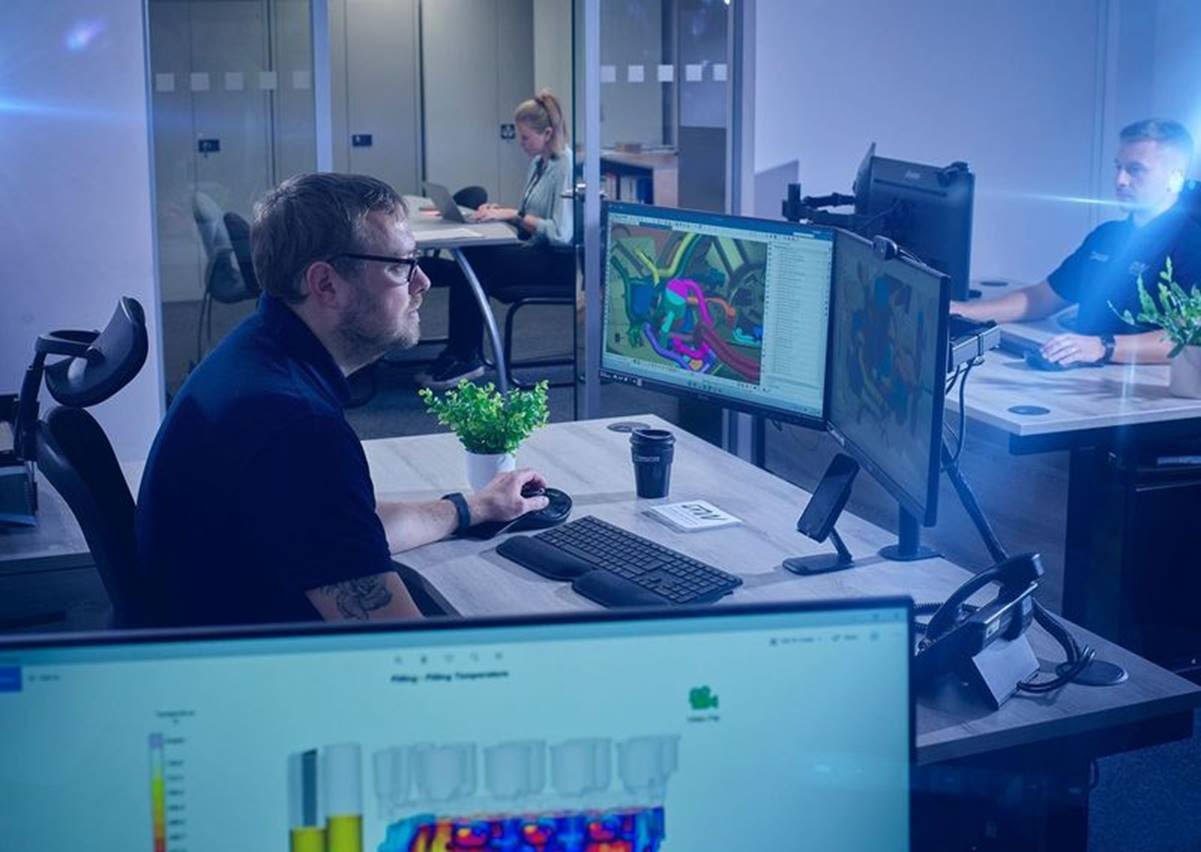
Climate change is here. This is but one of the grand challenges facing the world and, not surprisingly to some, Castings will play a key role in enabling technologies to drive solutions whether this be light-weighting, complexity or universal recyclability.
Imagine this: a component has reached the end of its useful life and within minutes it is remelted and cooled to an ingot ready to be used again. Better still if the intrinsic quality of the metal can be preserved at its original level by keeping it in a closed loop. Welcome to aluminium, a saviour of the manufacturing world.
Aluminium is, however, a bit of a troubled soul. It loves being oxidised, loves shrinking when solidifying and so to get the best from it GW employs real science, not the black arts, to design, compose and use aluminium in its many alloyed forms.
In this article, you will hear how GW is engineering solutions for specific products and markets whilst evangelising its sustainability through process modelling; virtual engineering of products and their creation processes to enable our Blue-chip customers to do the same with theirs. We are one in matching solutions to problems.
Much is spoken about digital twins. For us, this means process simulation; a set of software tools that model the sequence of casting from the liquid state, through the solidification process and lastly as a solid. At no point does Aluminium alloy behave in a homogenous state so computer modelling, whilst immensely powerful, only approximates the outcomes. This is where the physical twin is as important. At GW we drive both activities simultaneously ensuring that the inputs to the former are validated by the outputs of the latter. It’s a virtuous circle of learning and this has transformed the speed and accuracy of product development at GW.
Take for example a prototype Gigacasting. Perhaps 3m in length, 3mm in wall thickness and designed for use as a vehicle body structure where mechanical property distribution is customer-defined. The assumed initial conditions for solidification are unlikely to be calculated by computer simulation alone. This is because the precise boundary conditions of the mould and liquid metal vary, unlike the dataset, and so they need to be got, as quickly and as soon as possible. In the work plan our team produces physical data to validate key inputs such as metal velocity, mass and temperature distribution, heat transfer and flow path variations of which can massively alter the outcome of large and complex castings.
Once datasets are validated and uploaded, the digital twin outpaces the traditional iterative sampling process. Coupled with powerful computers this delivers very rapid, very accurate predictions that justify the engineer’s intended methods of manufacture ahead of those expensive tooling and production activities.
This is Design For Manufacture (DFM). An often-spoken acronym for casting development but one which often refers only to the shape and accuracy of the moulded part. At GW, DFM has a definite hierarchy that aims to quantify outcomes in terms of;
● Casting integrity: Ensuring good microstructures and minimised defects.
● Casting process repeatability: Simulating the entire process from pouring to heat treatment.
● Casting net weight: Determining useful vs not useful mass.
● Casting and machined part accuracy: Minimising process variation and tolerances.
The target of this is to make things right the first time. It also supports meaningful discussions with customers about what to expect from their cast parts. Castings are invariably heterogenous in properties so in the drive for optimum performance and lower weight knowing whether parts possess properties in the right locations or residual stresses in the wrong locations is paramount.
Take the Gigacasting analogy again: to have the confidence to crash test a vehicle made with prototype cast parts is only possible when there is confidence the casting is right. Being right is sustainable and it means that less time and useful resources are required compared to being just fast at multiple iterations.
Our CTO put it best when he said “The route to sustainability is to waste less by making things right first time. This means making things perform better while using less material and irrecoverable resources such as energy. We work extensively in the virtual world, using exacting datasets and process models before embarking on real parts. Where waste is unavoidable, the good husbandry of metal and sand media means that these are almost completely recycled without deterioration in quality.”
At GW we have been developing these predictive competencies for almost two decades. In the past 4 years alone this amounts to over 3000 product simulations across 750 new products. Castings get bigger, some get thinner but the neat laws that once were simple to reapply do not always scale proportionally. It’s a huge endeavour and one that never ceases to be justified as the size and complexity of customer designs change.
The need for a wider choice of castable materials that confer higher strength, sometimes at elevated temperatures, or which need to possess high ductility for crash energy absorption makes the list of alloys even longer. So then does our need to characterise the fullest range of 200 and 300 series alloys in their many heat-treated forms and produce our own datasets to correct the computer simulation results.
What's next...
We thrive on pioneering new technologies, and working in close collaboration to realise your full potential, so please don’t hesitate to contact us if you have any questions.
Related Posts
Grainger & Worrall races to King’s Award for Enterprise in Innovation with casting breakthrough
PRESS RELEASE
Why Sand Choice Can Make or Break Precision Casting
A Dynamic and Diverse Product Offering | Grainger & Worrall
The world is moving fast, and we’re keeping pace with highly adaptable castings that are enabling...