5 min read
A Dynamic and Diverse Product Offering for the Modern Age
By: Alex Grainger on Aug 14, 2024 4:43:25 PM
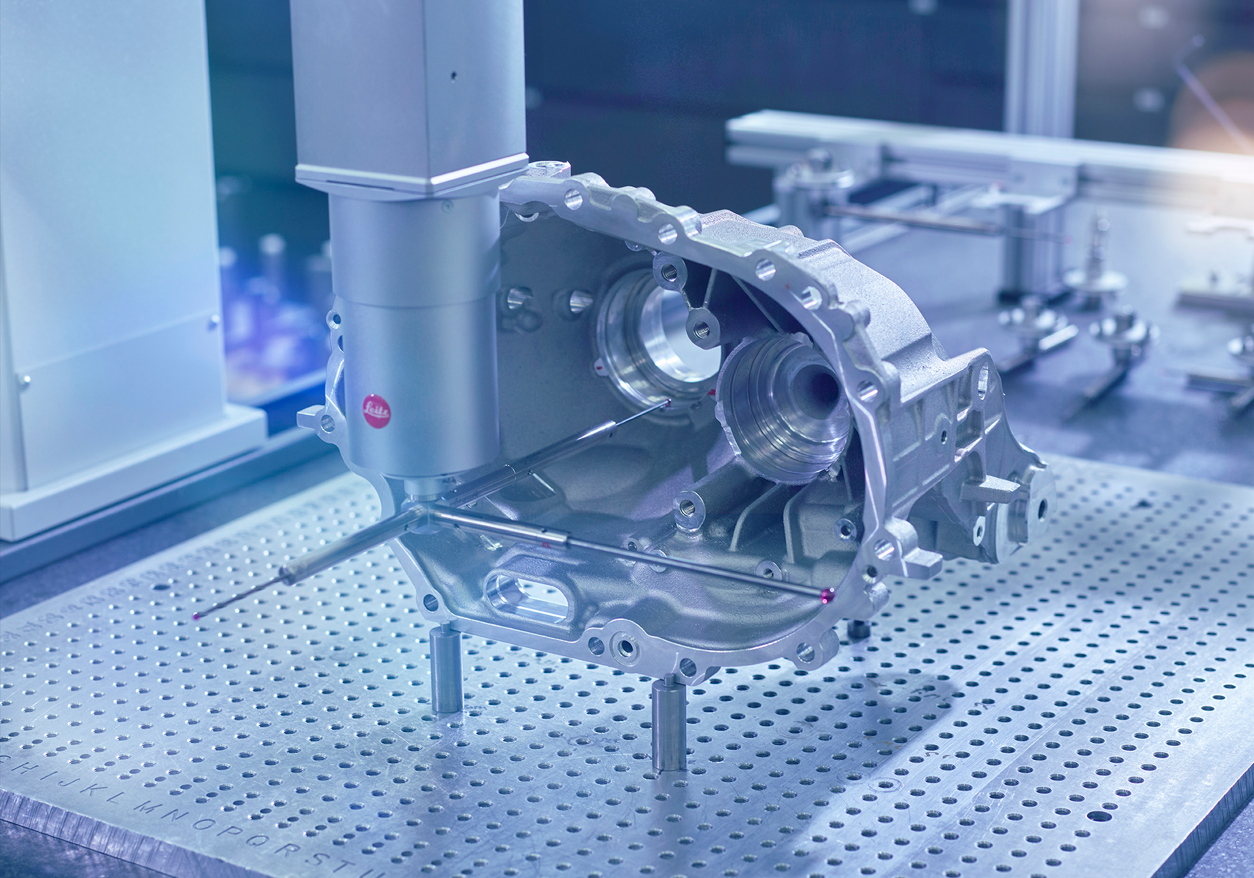
The world is moving fast, and we’re keeping pace with highly adaptable castings that are enabling some of the most innovative metal structure solutions.
As the automotive industry shifts its focus from traditional fossil fuels to sustainable alternatives such as hydrogen and electric, we’re powering the transition with advancements in lightweight, high-performance prototypes.
In this article, we’ll explore how we’ve adapted our service offering to support world-leading brands in a range of crucial sectors, including automotive, motorsports, marine, aerospace, defence and power generation.
A Complete Solution: Moulded by Your Vision
From one-offs to niche series production of up to 20,000 parts, we help you craft machines on the cutting edge of engineering. We’ve worked on everything from small intricate water pumps to 3m² structural castings, with the flexibility to adapt our diverse product offering and specialist knowledge to the unique needs of the project.
To help you get a better idea of exactly what we do, the parts we provide are usually split into three categories:
● Powertrain: Working on all sorts of different vehicles and machinery, we craft high-precision parts for the base engine, e-drive, intake charging and exhaust systems.
● Transmission: Our expertise in transmission parts spans a diverse portfolio of products and applications, including complex structural Bell housings and Gearboxes in exotic alloys.
● BIW structures: With leading-edge technology in building the leanest and greenest vehicles on the planet, we provide everything from giga structural castings to battery trays and chassis parts.
Along with revolutionary sand cast prototypes, we also have the machining capabilities to provide the ultimate high-precision finish, supporting Prototypes through to Niche volume series.
Wondering how these parts fit into your specific sector or application? Read some use cases below for some of the primary sectors we are involved in.

Powering a Greener Future in Vehicle Engineering
A need for sustainable fueled propulsion is shaping the future, with countries worldwide introducing dates for a permanent ban on the sale of new petrol and diesel cars.
To support our clients innovate and expedite the transition to new technologies we’ve evolved our rapid and agile prototyping process, with expert solutions to complex engineering challenges.
This includes innovating a new method for giga prototyping that uses a novel take on sand casting in place of the aluminium die-cast machine, removing initial challenges around cost, lead time and flexibility.
This enables us to create large, complex and lightweight BIW parts for EVs and other applications, reducing the need for multi-part assemblies and streamlining efficiency without compromising on performance.
Meanwhile, our fast make prototyping process allows us to shorten lead times dramatically, for Make Like Production parts in a matter of weeks – including all powertrain, transmission and BIW components.
With future-proof technologies and software, we can expedite sand casting prototyping in a range of alloys and complex geometries, from aerospace-run programs to motorsport solutions.
High Precision Parts to Accelerate Performance in Motorsports
When it comes to winning parts and ultra-precise aluminium components, our dedicated motorsports facility supports some of the world’s championship brands. Our castings appear on the grid across the majority of global race series, particularly in the powertrain and transmission space.
Many of these projects are ‘off-the-record’ to maintain confidentiality, but what we can say is we’ve developed a series of bespoke materials and processes to produce Formula One-grade castings that meet the high-integrity and complexity demands of the motorsports industry. This includes incredibly lightweight racing engines, that are focused on high performance and reliability, bespoke alloy compositions and specific heat treatment cycles to refine and optimise aluminium components.
We also use cutting-edge technology, simulation software, and CT scanning to ensure we can meet high tolerancing requirements, with 3D sand core printing to produce cores of virtually any shape, at speed. Our state-of-the-art machining centre with industry-leading capability can act as a complement to our casting solutions or alternatively, machine from billet, depending on the project requirements.
Launching the Lightest and Most Innovative Castings in Aerospace
From technical aviation powertrain and transmission components to castings that meet the extreme tolerancing requirements of outer space, we’re passionate about being a part of some of the world’s most exciting aerospace projects.
By developing unique alloy properties with specific techniques we focus on lightweighting, heat resistance, high strength and durability, to get your project off the ground with speed and agility.
Once the casting is complete, we use thorough validation strategies to meet stringent specifications set by you and allow for essential traceability of component parts.
High Integrity Designs to Bolster Defence
With niche expertise and a long history in the metal industry, we offer essential engineering innovation for the military sector in both aluminium and iron sand castings for air, land and sea.
From extensive research and development all the way to production, we lean on in-house expertise to craft powertrain and transmission parts that meet the unique needs of defence applications.
Our safety-critical precision castings are expertly optimised for lightweighting and performance, in machines from maritime and military vehicles to unmanned aerial vehicles, otherwise known as drones.
This results in better fuel management, manoeuvrability, and durability, with prototyping design flexibility to rapidly respond to design modifications with robust engineered solutions.
Sand Castings to Support the Race to Net-Zero
There’s a global power struggle going on – one that demands rapid action as we strive to meet ambitious but critical sustainability targets and move away from fossil fuel supplies.
Our incredibly fast and precise project delivery enables new technology across all sectors helping defeat their grand challenges with products borne from processes that are almost 100% recyclable.
Most importantly, we’re proud to be a part of the revolution to reduce global emissions by creating castings with a unique knowledge of the energy sector performance demands and supporting clients with creative and pioneering solutions.
.jpg?width=480&height=360&name=GWCasting%20Shoot24071650812%20(1).jpg)
What's next...
From recent growth in power generation programs (thanks to our unique capabilities in exotic alloys and engineering solutions), to our extensive portfolio of providing solutions for complex powertrain and transmission components, we have so much more to show you.
Get in touch to chat with one of our dedicated engineers about your project challenges.
Related Posts
Grainger and Worrall at The World Foundry Summit
This month, Grainger and Worrall's Engineering and Technology Director Keith Denholm, travelled to...
How Does Standardisation Affect Value Proposition?
How does the standardisation of automotive parts affect the value proposition? We asked our...
Meet George Harris, Supervisor for the Series Unit
In our latest video series Staff Stories, we've spent time with different people throughout the...