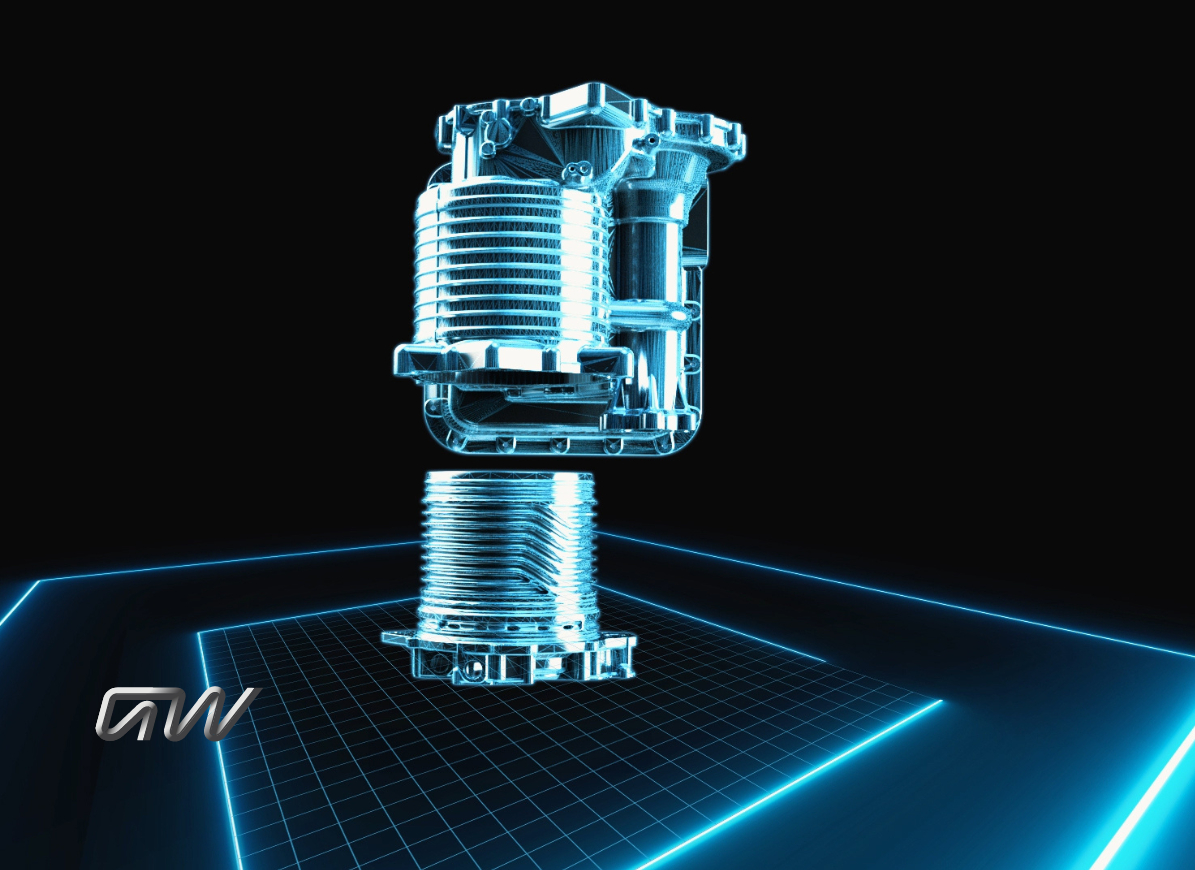
We engineer pioneering sand cast techniques to advance fast make aluminium prototyping, on a mission to move the world forward by taking innovative ideas into reality.
Our story starts with a rich history supporting the motorsports and high-end supercar industry with high-performance aluminium powertrain and transmission products. During the last decade, we’ve complimented our core offering by building on our extensive industry experience to support the critical path towards sustainability, including the Electric Vehicle (EV) market and other sectors driving societal change, with world-leading cast products.
This includes rapid solutions for parts such as large aluminium chassis structures, that need lightweighting, whilst still achieving the required properties, through to new alloys to support increased thermal conductivity for alternative fuels, with a full-service approach from initial feasibility studies up to niche series production.
Alongside our performance-enhancing developments in automotive, our prototyping process is trusted by some of the biggest brands in the motorsport, aerospace and infrastructure sectors – on projects so groundbreaking we’re not allowed to mention them by name.
Here, you can learn more about the benefits of fast make prototyping and find out how we’re expanding on our heritage expertise in aluminium sand casting to enable innovative complex concepts for a diverse portfolio of applications, to transform into reality.
What is Fast Make Prototyping?
Fast make prototyping is a form of rapid prototyping that focuses on speed without sacrificing performance and multiple design iterations to fine-tune the finished product. We use it to support a range of industries from automotive to aerospace, engineering complex aluminium castings for the latest and greatest machinery on the planet.
What are the benefits?
Quickly Meet Pre-Production Requirements
We adapt our service to meet your technical needs, whether you have a frozen design that just needs realisation, or multiple refinements to meet specific characteristics, we collaborate to achieve the right material properties with optimised dimensional tolerancing.
Fine-Tune Your Design With Speed and Flexibility
Modify and adapt your parts with agility by leaning on our deep knowledge and expertise. We do most of our design development in the virtual world to save time, waste and cost, with multiple changes to the simulation model before the casting prototype is realised.
Create Make Like Production (MLP) Prototypes Faster Than Ever Before
We specialise in make-like production prototyping that mirrors the properties of the end product, with high levels of accuracy on a range of specifications. Over the years, we’ve used creative engineering and state-of-the-art equipment to accelerate this process.
How We Transformed Fast Make Prototyping With Sand Casting To Produce Giga Structures
Sand casting has long been a fast and affordable way to create complex component prototypes in a range of industries, from motorsport to commercial off-highway. More recently, it also plays a pivotal role in prototyping a revolutionary new method for architectural car structures known as giga casting.
Giga casting allows you to manufacture much larger structural parts that streamline production, reduce costs and supercharge the sustainability of your finished vehicle. It’s key in the EV revolution, ensuring market-leading brands can craft lighter, leaner and greener vehicles, with lower production costs that can be passed on to the consumer – accelerating the transition from fossil fuels.
Giga casting is typically done with a large, high-pressure aluminium die-cast machine. While this has impressive volume capabilities for mass manufacturing, it’s limited by cost, lead time and flexibility when it comes to prototyping.
This is why we used proven in-depth know-how to develop innovative methods using sand casting for giga prototyping. Quick, cost-effective and offering the ability to craft complex prototype parts in almost any size, our process creates high-integrity, make-like production parts for your project, with multiple design iterations in tight timescales as required.
This is especially important in developing EVs, where complex, thin-walled giga castings can be engineered with unparalleled accuracy and consistency. This means we can now develop giga castings with walls of 3mm, and sometimes even less.
Our optimised process has revolutionised the conventional sand cast method, adopting 3D printed core technology if required to answer the need for rapid changes to the design.
The Future of Fast Make Prototyping at G&W
Despite global expansion into new markets, industries and territories, our commitment to personalised service, and engineering novel solutions at speed remains the same. In fact, our lead times have reduced even further, demonstrating our dedication to our core mission; helping you bring forward world-class products ahead of your competition, no matter how high-tech or complex.
Lightning-Fast Lead Times
Inspiration demands action, or else that spark can quickly flicker out. We specialise in a fully integrated prototyping solution with in-house capability. Initial engineering happens in our design office, from which we can quickly bring the visuals to life with 3D sand printing. Our end-to-end service also includes everything from quality assurance in our metrology suite to micron tolerancing in our state-of-the-art machining facility. This way, we can streamline the process from concept to reality.
Put simply, we can go from data to delivery in 8 weeks or less, with some recent products achieved in as little as 36 hours.
Creative Collaboration
We don’t just take your drawings and simply make them a reality. We work seamlessly alongside your team, offering decades of experience designing complex castings to fine-tune your prototype for a leading-edge finish.
The result is winning product development that might just change the world.
Outside-the-Box Innovation
When it comes to rapid sand cast prototyping, we’re the pioneers of problem-solving. Come to us with a complex technical challenge, and we’ll work in unity to find the right solution, with impressive speed and agility.
We have the creative and technical expertise necessary to develop pioneering prototypes that have never been done before, bringing your vision to life and overcoming any hurdles that arise along the way.
100s of New Product Introductions Every Year
We’re passionate about seeing products through from the spark of conception to their final, ready-for-market form.
Our process cultivates progress, not only for your brand but for a wider purpose, with a focus on disruptive technology and world-leading sustainability.
What's next...
Should you wish to learn more please get in touch, and we'll introduce you to one of our experienced lead engineers for further discussions.
Related Posts
From Iron Legacy to Aluminium Innovation | Grainger & Worrall
It’s been three years since we pioneered our first Giga casting. A revolutionary move for...
THE ENGINEER & RICARDO DISCUSSION
Keith Denholm, our Engineering and Technology Director joins with other industry experts to discuss...