4 min read
From Iron Legacy to Aluminium Innovation: A Market-Leading Transformation of One of Our Facilities
By: Alex Grainger on Jun 26, 2024 2:03:51 PM
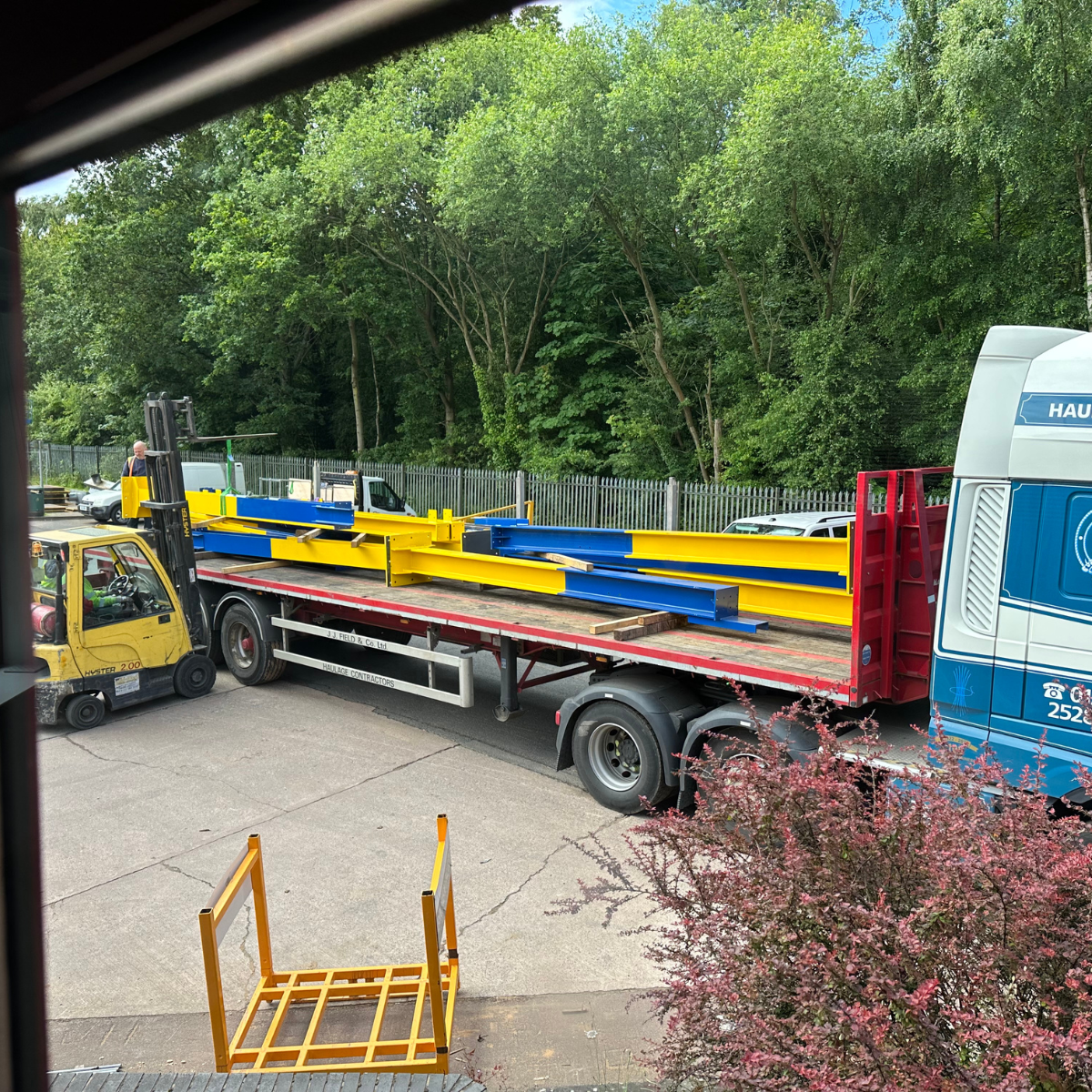
It’s been three years since we pioneered our first Giga casting. A revolutionary move for automotive manufacturing, Giga casting enables us to craft large and lightweight aluminium parts in a single cast.
Streamlining efficiency and reducing lead times, Giga casting is a key enabler for the future of vehicle engineering, and we’re making it happen. This cutting-edge technology runs in parallel with our pioneering large structure prototyping capabilities, allowing us to offer ever-more complex, state-of-the-art solutions to the world leaders in automotive engineering.
To support the ever-growing demand for our aluminium Giga/large structural casting capability, we’re investing in a new facility designed exclusively to support some of the most advanced electric vehicle (EV), defence and aerospace engineering projects on the planet.
In this article, we’ll give a quick history of the Giga casting landscape, how it works and how we’ve transformed the process. We’ll also look at how we’re transitioning from a heritage iron foundry and increasing the capacity and capability of our aluminium prototype offering – with a technology-focused, world-leading aluminium sand cast facility.
A Quick History of Giga Casting
Giga casting is currently one of the biggest buzzwords in car manufacturing. While the term itself has been popularised by the most prominent name in Electric Vehicles, Giga casting is a technology born of a universal trend for lightweighting and lowering the carbon footprint of our vehicles.
Put simply, Giga casting streamlines manufacturing by integrating what would have been multiple different components into one single aluminium casting, which can serve as the entire front or rear underbody of a vehicle. It’s especially useful in EVs which require large and complex structural parts to accommodate their batteries.
Typically Giga casting makes vehicles both cheaper and more efficient, with fewer welds required, shorter assembly lines and higher dimensional accuracy. Lighter vehicles are also inherently more sustainable, increasing battery range to support the global transition to EVs.
Previously, the problem with Giga prototyping was that it required a large, high-pressure aluminium die-cast machine, which is limited by cost, lead time and flexibility.
To solve this problem, we devised a leading-edge method for Giga prototyping that uses traditional sand casting in place of the die-cast press, offering lightning-fast lead times for the original equipment manufacturers (OEMs) that are innovating ahead of their competition.
So Cutting-Edge It's Classified
With the market trending towards leaner and greener EVs, we’ve been creating Giga prototypes for some of the biggest names in the industry.
Due to this ever-increasing demand, we’ve decided to invest significantly into our facility to maximise our aluminium capability and ensure we can continue to support our clients with cutting-edge product development.
The Bigger Picture of Giga
While Giga casting is helping revolutionise automotive manufacturing, complex large aluminium castings continue to be a transformative tool for manufacturing in a range of heavy machinery industries, from defence to aerospace.
We harness cutting-edge material science to achieve exceptional high strength-to-weight ratio properties with our aluminium alloys, maximising the benefits of lightweighting but also providing the necessary key characteristics for performance.
Our specialist prototyping capabilities mean we can help innovate across industries, increasing engineering flexibility and reducing manufacturing costs with large aluminium structures, tailored to the needs of your project.

The Future of Large Structural Casting at G&W
We’re already known for our innovative and unique processing capabilities, and now we’re adapting with speed and agility to finetune the Giga and aluminium casting process for all our current and future partners.
Tripling Our Giga Casting Capacity
Here you can see some sneak peek images of the space for our new state-of-the-art aluminium facility. These initial progress photos show the area that has been cleared ready for the transformation, with work starting in earnest early this summer.
Watch this space to see how we build on our Giga casting expertise to develop a futureproof aluminium facility for the modern age of machinery manufacturing. The new facility is designed to complement our existing offering in aluminium, maximising capacity for both Giga casting in vehicle manufacturing as well as large aluminium parts for defence and aero applications.
A Dynamic New Direction
We're already a few roads ahead as dawn breaks on the EV era. We’ve enlisted a fresh-thinking new team to support our market-leading brand through the transition, with an outside-of-the-box approach that creates new opportunities for OEMs.
We collaborate with creativity to design and redefine your Giga prototypes, pioneering some of the most groundbreaking global projects with ultra-fast prototyping and product development.
Refined Dimensional Accuracy
Our innovative Giga casting prototyping process allows us to develop complex, thin-walled castings with high accuracy and consistency, 3mm or less.
We have engineered techniques to enhance the overall dimensional capability to target ‘make like production’ results to support our customers in testing the concept ahead of moving into production.
Our commitment to crafting thin-walled Giga prototypes without compromising dimensional accuracy enables you to build on the possibilities of this advanced technology for all kinds of structural body-in-white components.
What's next...
Interested in learning more about our new facility or Giga casting capabilities? Simply get in touch, to talk through your ideas with one of our lead engineers.
Related Posts
What Is Fast Make Prototyping? | Grainger & Worrall
We engineer pioneering sand cast techniques to advance fast make aluminium prototyping, on a...
Material Innovations in The Aerospace & Automotive Industry
When it comes to materials, the aerospace and automotive industries have more in common than you...
FOLLOWING THE FORMULA – DRIVING INNOVATION IN MOTORSPORT
Recent changes to Formula One regulations have led to significant innovation and development in the...