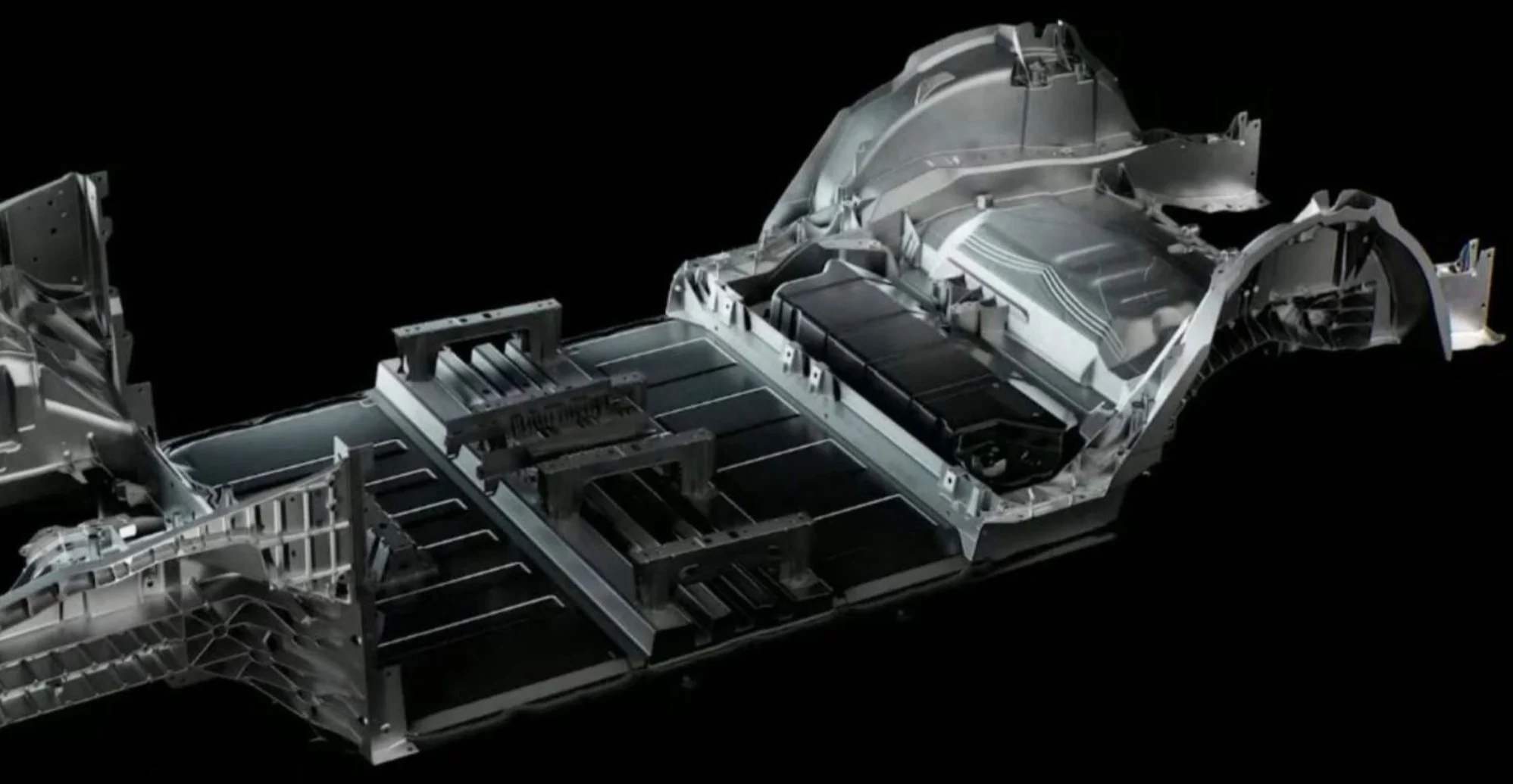
You might have noticed that IDRA’s Giga press is gaining increasing coverage regarding its potential to revolutionise the automotive sector.
By casting chassis components in one piece, it is pushing the boundaries as to what can be achieved in production speed, cost saving and part count reduction with innovative approaches to casting capability.
Casting half a car in one step brings some impressive benefits, including reducing part count for a car from over 100 to just 3. With a cycle time of circa 90 seconds, it is possible to cast approximately 1000 parts per day. Companies such as Tesla believe that the giga casting will help drive electric vehicle adoption as prices can be driven down by reducing assembly costs and increasing production rates.
Check out this video of how the Giga Press operates.
Read more about controlling mechanical and material properties with alloy selection
Find out more about the sand casting process
Innovation and technical expertise for EV prototype castings
This advance in casting technology presents exciting opportunities for the EV automotive industry, driving technical innovation and potential to hit the price points required for mass adoption. A vital stage to achieving successful mass production of the large structural parts that can be produced by the Giga Press is prototyping. It’s here that sand casting offers a number of advantages for developing EV prototype components.
With the correct expertise, sand casting can produce prototype castings which exhibit the production characteristics that might be observed in high-pressure die casting environments. This Make Like Production approach to prototyping can help shorten product development cycles significantly.
How do you prototype these large structural castings?
There are several factors to consider in the prototyping stage to achieve a high-integrity prototype sand casting. These include alloy selection, process design, component design (including topology) and optimising for solidification rates to achieve the material properties that will be required in EV components such as battery trays, EDU housings, front/rear underbody structural parts, etc.
Tailoring prototype sand castings to mimic die-cast parts can be achieved using a combination of techniques such as;
- Bespoke alloys such as an aluminium-silicon can be created to match properties achieved in die casting for high-volume production. This allows mitigation of heat transfer in sand casting moulds, enabling controlled solidification rates without the need for heat treatment. This is analogous to the high cooling rates of die casting, producing sand cast prototypes with the required properties of tensile strength, yield strength and elongation.
- Process design at the prototyping stage can replicate the properties achieved in high volume die casting. Designing effective runner and feeder systems to control the rate of solidification in the prototype casting is vital, matching the results achieved with high-pressure die casting in high volume production.
- Component design is optimised at the prototype stage. This can include considerations such as split line placement, draft angles, hot spots and junctions to ensure equal solidification and feed rates of the metal.
To wrap up
The innovation shown in the Giga Press highlights exactly what can be achieved when you understand the fundamentals of a manufacturing process. Sand casting can play a significant role in the prototyping stage of new product development. It enables engineers to drive innovation with technical knowledge and material selection to produce prototype components with production properties.
There’s plenty of variables that can be controlled and altered within the sand casting process to tailor a part to your specifications. To find out more, download our free ebook, the Basics of the Sand Casting Process.
You might have noticed that IDRA’s Giga press is gaining increasing coverage regarding its potential to revolutionise the automotive sector.
By casting chassis components in one piece, it is pushing the boundaries as to what can be achieved in production speed, cost saving and part count reduction with innovative approaches to casting capability.
Casting half a car in one step brings some impressive benefits, including reducing part count for a car from over 100 to just 3. With a cycle time of circa 90 seconds, it is possible to cast approximately 1000 parts per day. Companies such as Tesla believe that the giga casting will help drive electric vehicle adoption as prices can be driven down by reducing assembly costs and increasing production rates.
If you have not seen it already, check out this video of how the Giga Press operates.
Innovation and technical expertise for EV prototype castings
This advance in casting technology presents exciting opportunities for the EV automotive industry, driving technical innovation and potential to hit the price points required for mass adoption. A vital stage to achieving successful mass production of the large structural parts that can be produced by the Giga Press is prototyping. It’s here that sand casting offers a number of advantages for developing EV prototype components.
With the correct expertise, sand casting can produce prototype castings which exhibit the production characteristics that might be observed in high-pressure die casting environments. This Make Like Production approach to prototyping can help shorten product development cycles significantly.
How do you prototype these large structural castings?
There are several factors to consider in the prototyping stage to achieve a high-integrity prototype sand casting. These include alloy selection, process design, component design (including topology) and optimising for solidification rates to achieve the material properties that will be required in EV components such as battery trays, EDU housings, front/rear underbody structural parts, etc.
Tailoring prototype sand castings to mimic die-cast parts can be achieved using a combination of techniques such as;
- Bespoke alloys such as an aluminium-silicon can be created to match properties achieved in die casting for high-volume production. This allows mitigation of heat transfer in sand casting moulds, enabling controlled solidification rates without the need for heat treatment. This is analogous to the high cooling rates of die casting, producing sand cast prototypes with the required properties of tensile strength, yield strength and elongation.
- Process design at the prototyping stage can replicate the properties achieved in high volume die casting. Designing effective runner and feeder systems to control the rate of solidification in the prototype casting is vital, matching the results achieved with high-pressure die casting in high volume production.
- Component design is optimised at the prototype stage. This can include considerations such as split line placement, draft angles, hot spots and junctions to ensure equal solidification and feed rates of the metal.
In conclusion...
The innovation shown in the Giga Press highlights exactly what can be achieved when you understand the fundamentals of a manufacturing process. Sand casting can play a significant role in the prototyping stage of new product development. It enables engineers to drive innovation with technical knowledge and material selection to produce prototype components with production properties.
There’s plenty of variables that can be controlled and altered within the sand casting process to tailor a part to your specifications. To find out more, download our free ebook, the Basics of the Sand Casting Process.
Related Posts
How does sand casting support giga casting prototypes?
Within the automotive industry, giga casting is a relatively recent technology. As a result, there...
Speed, accuracy and flexibility : how sand casting supports prototyping
How does sand casting support rapid prototyping projects? And just how fast is the process?
4 Ways Sand Casting Supports Electric Vehicle Manufacturing
Achieving global aims of carbon-neutral transport is a huge challenge. Electric vehicles are set to...