4 min read
Supporting the Fuels of the Future With Cutting-Edge Material Developments
By: Alex Grainger on Jul 23, 2024 4:56:47 PM
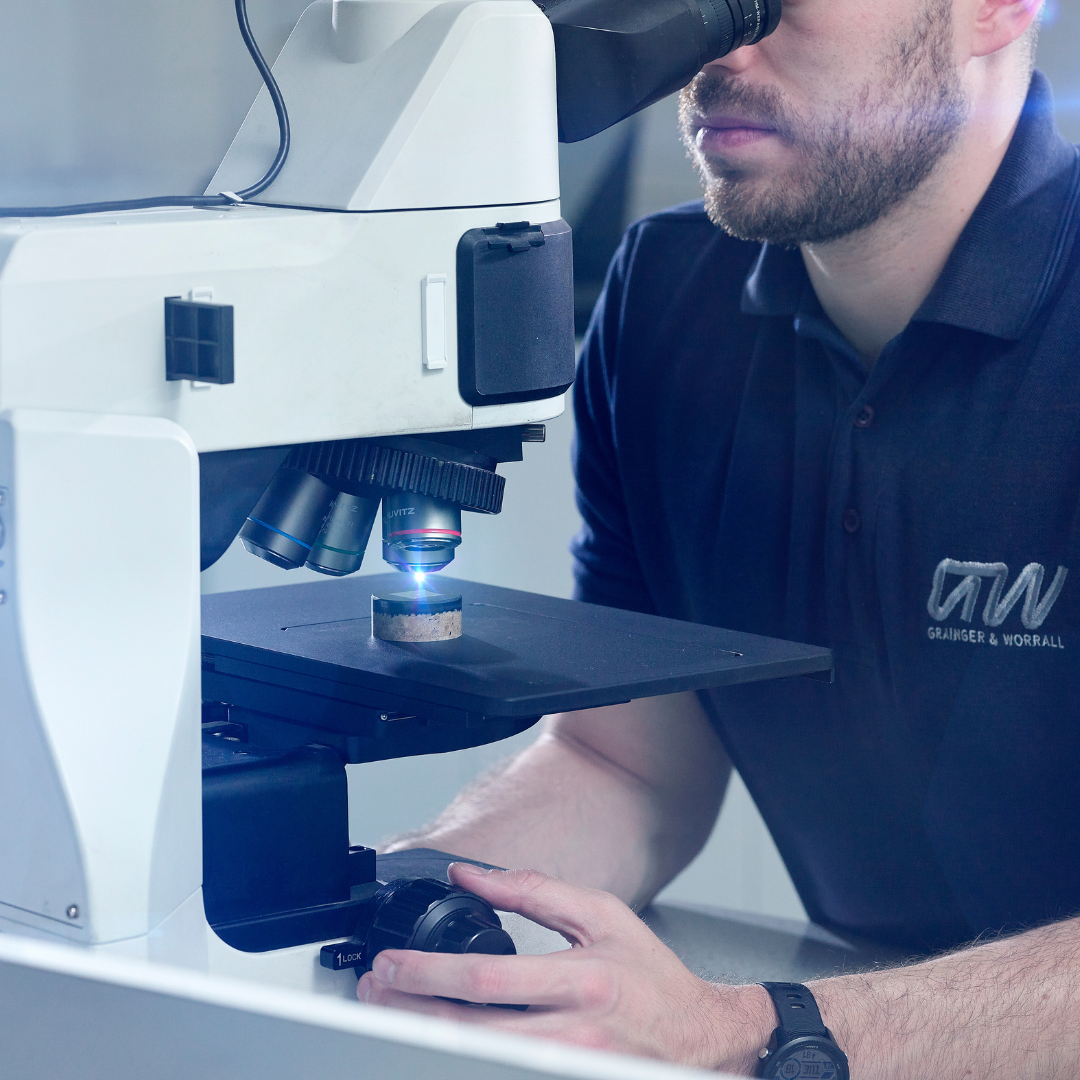
As the world transitions from fossil fuels to sustainable alternatives, we’re pioneering a new era for the automotive industry with cutting-edge material developments.
We’ve always been at the forefront of high-integrity structural castings, but now, we’re turning our attention to the latest and greatest technologies to support the complex manufacturing requirements of hydrogen and electric vehicles (EVs).
This includes everything from state-of-the-art solutions for powertrain structures to high-performance alloys for motorsport and aerospace applications. We’ve also transformed the prototyping process for body structure type Giga castings, which combine multiple vehicle components into one large and lightweight casting, accelerating advancements in body-in-white (BIW) manufacturing.
In this article, we’ll explore some of the latest material developments at G&W, and how we’re shaping the future for sustainability and alternative fuels.
Optimising High-Quality Aluminium Alloys
When it comes to large-scale structural BIW castings, we tailor our solutions to unique project requirements, including unique alloy chemistries to answer your specific goals and objectives.
From lightweighting and thermal conductivity to improving strength and maintaining ductility, we work collaboratively to improve on the specified properties and produce make-like-production prototypes for your project.
Our highly customised, collaborative delivery process supports the manufacture of parts in 300 (AlSi) and 200 (AlCu) series type alloys. As part of the consultation and engineering process we tailor alloy compositions and capabilities to the demands of the application. For example, 200 series alloys, where high strength properties of up to 480MPa UTS have been repeatedly achieved. Conversely in 300 series where ductile properties were required, obtaining elongations greater than 15%.
We are able to offer advanced heat treatment development strategies to further enhance and improve mechanical properties. We also work to optimise dimensional stability and introduce techniques to relieve residual stresses as part of our established alloy portfolio.

Revolutionary Research and Development
We use one of the leading simulation software packages for casting design and optimisation, allowing us to prototype properties in a virtual world before production and reduce unnecessary weight in large structures. This ensures we get things right the first time and streamlines the entire engineering process, for accelerated innovation, every time. We have revolutionised this technology by creating our own thermal transfer datasets to enhance accuracy.
As part of our continuous research and development strategy of our alloy portfolio, we continue to utilise new industry technologies. We have approached this from an ICME, Integrated Computational Materials Engineering, perspective and in combination with extensive trials have been able to achieve new transferable capabilities.
Advanced Validation Capabilities
There is a peerless Imaging capability at GW which includes CT scanning, Optical scanning and Digital X-Ray.
CT scanning allows us to check wall thickness and map even the smallest details preventing possible flaws in the manufacturing process later down the line. We then utilise endoscopy analysis and, specific dye penetration to identify and validate any subtle surface imperfections.
Supporting State-of-the-art EV Engineering With Creative Collaboration
Our approach is guided by your ideas and inspiration, taking our expert knowledge in crafting highly complex castings to develop new, more sustainable solutions. We tailor our approach to meet your specific objectives, from circular economy initiatives to ultra-high-performance alloys.
Meanwhile, our custom material compositions are carefully optimised to meet key component functional attributes e.g. crash response deformation.
The Latest Developments at G&W
With an innovative approach and some of the most efficient equipment in the world, we work hard to stay at the forefront of structural aluminium casting. Here are a few things we’ve been doing recently to maintain our leading edge:
Lighter, Stronger, and Optimised Castings
Some of our latest work includes ground-breaking parts for some of the world’s leading vehicle manufacturers, who trust us to deliver high-performance prototypes to the desired specifications.
This includes high-integrity, thin-walled castings for rapid prototyping aluminium parts across automotive, motorsport, defence, power generation and aerospace applications.
Superior Metal Quality and Preparation
We employ both gravity and low-pressure pouring techniques to cater for extremely wide-ranging material and component sizes. All have been optimised to preserve maximum material quality and the low-pressure system includes rollover, demonstrably the most consistent sand casting system available.
With a deep understanding of clean metal preparation, pouring, and solidification mechanics, we can apply our solutions to the widest range of complex metal shapes and components, reducing overengineering and maximising production efficiency.
HIP and Heat Treatment to Optimise Performance
By using advanced heat treatment methods, we can tailor process parameters by means such as Differential Calorimetry. Our in-house facilities give us the freedom to develop optimum heat treatment cycles for material properties, dimensional accuracy and the least residual stress.
Where applicable we also have developed options for Hot Isostatic Pressing (HIP) treatment to provide increased properties such as integrity, durability, strength, and corrosion resistance.
Make Like Production Material Quality
By We know how important it is for you to get your product to market quickly, which is why we focus on fast make prototyping without compromising on Make Like Production (MLP) quality.
This means selecting materials and processes to match functional attributes regardless of the destination production process Cosmetic and surface conditions can be the focus for enhancements by the many coating and sand media options available.
What's next...
Want to talk to one of our leading engineers about your material development challenges or simply chat through some ideas? Simply get in touch to learn more.
Related Posts
CASTING THE FUTURE, INSPIRATION FOR THE NEXT GENERATION OF ENGINEERS
Graduate and apprenticeship programmes:
SHROPSHIRE COMPANY BEGINS SEARCH FOR ENGINEERS OF THE FUTURE
Shropshire-based precision castings company, Grainger and Worrall (GW), is looking for the next...
GRAINGER & WORRALL TO RECEIVE PRESTIGIOUS MULTI-MILLION POUND DEVELOPMENT FUNDING
Grainger & Worrall, the world’s leading total casting solutions provider, has been awarded a £1.2m...