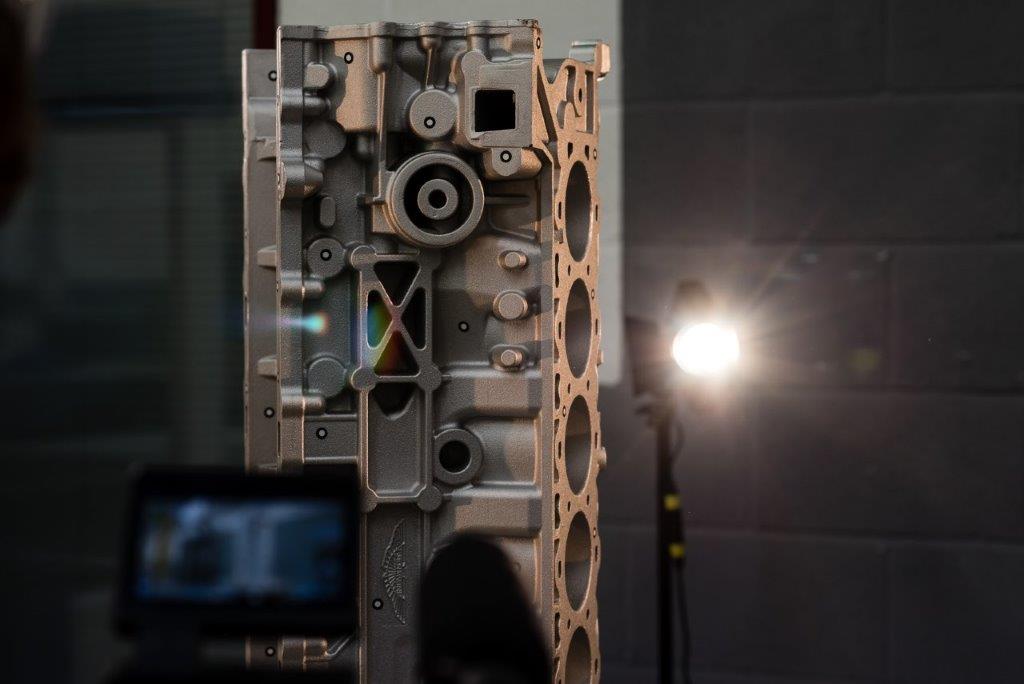
The automotive industry’s response to emissions legislation and consumer expectations has resulted in considerable changes in engine technology recent years. Light weighting and downsizing have led to smaller and more efficient engines, returning fuel economy and emissions figures that have plummeted in the past decade. Throw into the mix the use of CAD software for the design of engines and we’re truly in high-tech territory.
However, one area of the engine-making process engine casting- on the surface still seems very traditional. The use of sand cores, for example, seems to place engine castings firmly in the 20′” century, but that is deceptive.
“We can now virtually engineer and design using CAD. We can produce tooling and sand cores direct from digital data sets,” states Keith Denholm, engineering and technology director at Grainger & Worrall. “We can make castings in the classical way, but we can then take those parts and put them through very capable technologies such as CT, optical scanning and laser scanning. We have all those technologies, which enable us to do the verification and certification processes very quickly.
“Having engines that can be smaller, shorter etc, requires that materials be more predictable in their delivery, processing and manufacture. and ability to be modelled. Engineers no longer need to just hope for the best, because they now have data with which to design more aggressively.”
CAD has also contributed to the design of castings, as Edmund Burton, senior design engineer at llmor Engineering, explains: “When I started in the industry, most castings were drawn, so you had to work out in your brain what you wanted to show on paper. You thought in 3D and displayed it in 2D for the pattern makers, who then had to convert into 3D pattern equipment. So there were two levels of translation.
“Now with 3D CAD you can easily show your 3D model on screen, so it’s easy to get a 3D form of what you want to produce. And with all the pattern makers now using CAD, they can take your model and put it directly into the pattern equipment. Nothing is lost in translation.”
Software also helps in the analysts of the casting process itself, as Ken Miller, vice president of Hitchiner Manufacturing in the USA, tells us. “The big thing we’re really using is a lot of engineering evaluation tools. We’ve got tools that can analyse our casting process and help us understand where defects might occur. This process has really come a long way. We have fewer cycles in prototypes, so we don’t have to physically make parts to prove them out. We can prove out a lot of this type of development early on.
“We’re using a tool that models the solidification of the molten metal. Another we’re using analyses the turbulence of flow.”
These new technologies are leading to greater tolerances. Denholm says, “Things like strength and porosity are subject to variability in the process. Our task is to narrow those tolerances. That comes down to controls on the shop floor: having appropriate controls of metal control, metal temperature and chemistry compositional checks. We deploy spectrometry, which is quite familiar as a technology, with every melt preparation. We understand the chemistry before we cast and we are able to check gas levels as well.
“There are other things we have to control which require thermal analysis during the process,” continues Denholm. “This allows us to ensure that we have the right microstructure at the point we pour the metal into the mould. All these things are intended to ensure that, in the long-term tests on material performance and consistency, the tolerances are narrow”
“Casting, as an industry, might be seen as fire and brimstone, smoky rooms and things like that, but actually it’s not the case. Castings are very high-tech. They require high-tech processes to make them work and, when you do, you get a very high-tech product at the other end. The market we operate in – prototyping, motorsport and prestige or niche marques such as sports car manufacturers – exemplifies the opportunities that are here today and will continue for some time, in terms of helping push forward various castings technologies.
The use of new technologies and techniques is benefiting everyone – from casting companies to the OEMs and Tier 1 suppliers they work with to end consumers – as continual improvements are achieved with the internal combustion engine.
“We can make the fine, very detailed and very precise castings that our customers’ engineers need to make new devise that can enhance the performance of their engines,” says Miller. “There is a clear demand for fuel economy and people are willing to pay for it. We can deliver what is needed – thinner walls and lighter weight. We do a lot of light weighting. We compete against forging and we can be more precise and put metal where it needs to be to provide the strength. That’s has a big benefit, because we can get equivalent or better strength with less metal, and it helps save costs.”
Technology hasn’t totally eradicated more traditional ways of working, however, as Denholm explains: “A lot of the casting we are producing have to be machined into a finished product. In a powertrain, most of the parts have to be machined. The tolerances, the limits of the fit, the bearings, the joints, the functional surfaces- can’t be made using CAD. Those processes, while there are technological advances in machining, remain familiar. We’re still deploying a lot of machining -70-80% of our sold product is machined. The technology we’re employing is improving, in terms of its capability and accuracy, but it’s still the same approach. It’s still subtractive manufacturing, where you start off with a raw part and cut bits off.
“For a while that will remain the way, because it’s very reliable, relatively easy to define in terms of capacities, and relatively low cost because of those factors.
“This method will be challenged in time. There will come a time when additive manufacturing will negate the need for a lot of machining. There are some fabulous technologies being developed, but they haven’t been scaled yet to be economically or practically available to support the industry. But in 50 years a lot of the subtractive manufacturing technologies, which are wasteful, will be replaced by addictive manufacture, where you build a part with the precision that will enable some of them to remain unmachined.”
Those processes are still expensive for large-scale manufacturing, but in the motorsport sector, where Ilmor operates, that future is now.
“Quite often you can print the cores – a bit like rapid prototyping. You send your model to the foundry, which has a big vat of sand and resin in it,” says Burton. “The resin is activated by a laser, so where you focus the laser the resin will set. The laser traces out the shape of the core and then you merely shake it out from the loose sand and you’re left with this printed, solid core. It hasn’t required any pattern equipment to make it, so it can be built straight into your core pack and used. If someone was primed, you could send them a model one day, print it the next day and create the casting the following day. It never works like that, but theoretically it could take weeks out of the process.”
‘Fire and brimstone’ and ‘smoky rooms’ might still be what we associate with the casting industry, but technology has in no way passed it by. Additive layer manufacturing will force further changes in the decades to come, making processes easier and more automated.
Related Posts
GRAINGER & WORRALL MOVES UP THE RANKS AT MIA
Rounding off a year that has seen significant machinery investment and continued major OEM...
Will Mega Casting Influence Non-Automotive Industries?
Will mega casting have a role to play in non-automotive industries? We asked our Engineering and...
What Is Fast Make Prototyping? | Grainger & Worrall
We engineer pioneering sand cast techniques to advance fast make aluminium prototyping, on a...