7 min read
CT SCRUTINY A CASTING COMPANY THAT REGARDS COMPUTER TOMOGRAPHY AS A GAME-CHANGER
By: John Smith on Mar 24, 2016 9:00:00 AM
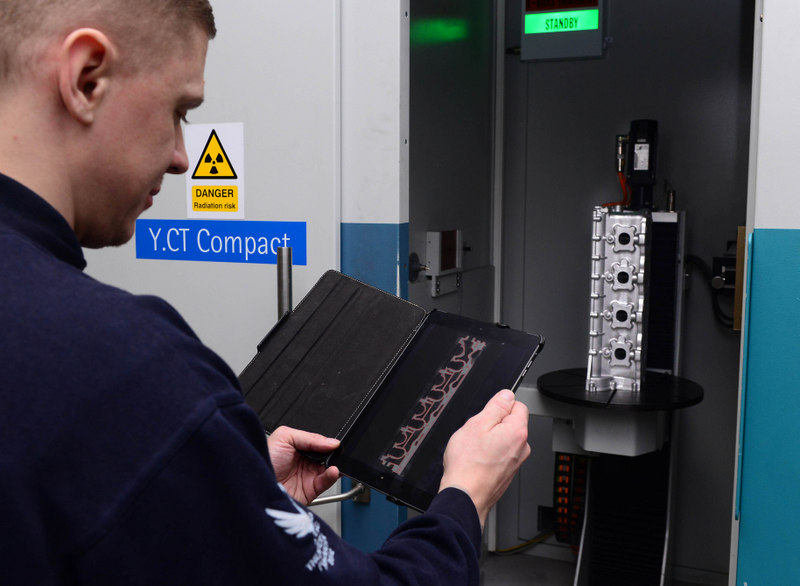
As suppliers aim to meet quality and reliability benchmarks, AMS speaks to a casting company that regards computer tomography as a game-changer
The time has long gone when automotive suppliers – certainly those at Tier 1 level – did nothing but supply parts to order. Now they must also frequently act as partners in component design and development, responding to orders almost instantly in a context where quality is simply taken as read.
That pithy summary of what is required to survive in that business area today is provided by someone who should know – Edward Grainger, director of UK-based castings supplier Grainger & Worrall. The privately-owned firm employs some 600 people in the development and production of castings for use in engine, transmission and structural applications.
Grainger concedes that the company’s business culture might be slightly “conservative” but its attitude to the use of technology is not. This is reflected in numerous ways in its design and manufacturing operations. Not only are there, for instance, three different CAD systems – from Dassault Systemes, PTC and Siemens – but also ultra-sound, X-ray and computer tomography (CT) hardware, each of them types of technology that despite their more immediate association with medical use are, as Grainger points out, also well-established industrial tools.
CT has, in fact, been a fact-of-life at Grainger & Worrall for the last ten years. It was introduced because the company found that the combination of ultra-sound and X-ray techniques it was already using could not by itself satisfy the targets the company had to meet in terms of quality control and product reliability. Grainger explains that the tiniest of imperfections in a casting can at times have the most deleterious of consequences and that when the company became aware of a means of detecting them more accurately then failure to implement the relevant technology was an unacceptable option. “It was not a risk we were prepared to take,” he says, flatly.
No more destructive testing
At a more pragmatic level, the technology has also enabled the company to reduce drastically the need to test expensive castings by destructive methods. It has, Grainger says, effectively abolished any need to destroy parts in order to check them for imperfections or dimensional accuracy. The only occasions when destructive testing is now necessary are “when we have to get inside the part in order to carry out mechanical performance testing to determine such factors as tensile strength or residual stress in a particular area.” He hazards the estimate that CT saves the need to cut up perhaps two to three castings in each one of the prototyping projects it carries out obviating, therefore, the need to destroy the better part of two thousand otherwise usable castings each year.
Moreover, as Grainger also explains, quite apart from the sheer waste involved in being unable to sell an expensively produced casting if it has been destroyed, “cutting up parts” is not necessarily a reliable means of quality control. Given that the underlying objective is to ensure that the production process can actually produce parts that conform to specification on a consistent basis then a selective procedure is always questionable. As he says: “At what point do you stop cutting up parts and decide that the process is OK?”
The fundamental capability that CT brings to the company is, says Grainger, that of being able to pinpoint precisely in three dimensions just exactly where inside a casting a defect as small as a bubble or grain of sand might be located. X-rays, as he explains, may be able to detect such imperfections but cannot determine exactly where they are because they examine the whole volume of a casting simultaneously. “They cannot provide an absolute,” he states, adding that their interpretation therefore required considerable subjective input from suitably experienced staff.
CT, in contrast, examines an object in a series of sequential ‘slices’, which means that not only the size and nature of an imperfection can be identified but also its location. Though it does not remove the need for skilled interpretation the technology is, therefore, more objective in its own right.
That objectivity, moreover, is also manifested in another capability it provides – that of precise metrology. “It can measure a part exactly,” explains Grainger, an obviously useful attribute when the parts involved will have gone from a molten to a solid state during manufacture.
CT is an integral part of the inspection portfolio
Accordingly, Grainger & Worrall made an initial investment of some £350,000 in its first machine, an outlay repeated three years later when a second identical machine was added. Total investment in the technology over the last decade has been, Grainger estimates, around £750,000.
Utilisation, more pertinently, is intensive. The two machines are operated on a 24-hour basis and do so as both quality control and development support tools. On the former count, Grainger says that for a customer requiring a small batch, engines with extreme reliability requirements (for instance, a Formula One team) the use of CT as a 100% inspection technique would be a “no brainer”. The cost-benefit ratio would simply be overwhelming and use of the machines will accordingly be a contractual requirement.
On the latter count, Grainger says that machine utilisation can often be more ad hoc. Development engineers, he explains, often take a part to one of the CT machines to see if there might be a timeslot to check some point of detail that may have been identified as potentially problematical by X-rays or conventional coordinate measurement. Hence, to a significant degree, the company’s use of CT is as an integral part of the portfolio of inspection and analysis techniques rather than as an isolated procedure.
An intensive CT analysis routine might typically involve examining a part in several hundred ‘slices’ each maybe 1mm in thickness though a range of 0.75-2.00mm is available. Grainger says that the procedure would then probably take one minute per slice so a workpiece 300mm in thickness would spend around five hours in a CT machine. But in such an instance the procedure would very likely be carried out on an unattended overnight basis.
The output from that process would, Grainger says, comprise two main elements. The first would be a ‘tomograph report’ that would precisely identify the nature and location of any imperfections down to a size of just 0.2mm in width. The second would be an accurate 3D representation of the part’s external and internal geometry that could be compared with the relevant 3D CAD reference data to ensure that the manufactured part conformed to the design intent. The particular importance of that is that engine castings contain internal channels that simply cannot be checked otherwise by an external, non-destructive method.
In turn, adds Grainger, that capability does not just check the integrity of the initial casting process but can also help ensure that subsequent machining will not in any way compromise product quality. The precise location of a drilled hole, for example, could be ‘tweaked’ slightly to ensure it does not aggravate what might otherwise be an acceptable slight imperfection.
Moreover, the output from the process can be used as the basis for interaction and discussion between the company and a client on a remote basis. Grainger says clients can easily log in remotely to the company’s own internal network or be sent a file of the particular area of interest. Indeed, Grainger identifies the increased ease with which such interaction can be carried out simply as the result of developments desktop computing and wide area networking as one of the key ways in which the utility of the technology has increased since it was first installed.
Humans check the ‘slices’
The actual machines – two XYLON CT Compact units – sit next to each other to one side of a large room out in the main factory complex. They are under the immediate supervision of metrology manager Gary Breech, who says that they can deal with workpieces up to maximum dimensions of 500mm in diameter and 750mm in height. In practice, though, the capabilities of the machines mean that at the largest sizes only aluminium parts are involved. Iron parts tend to be limited to maximum widths of 100mm. He also confirms that after workpieces are loaded manually onto the table inside each machine and the door shut operation is then a completely automated procedure.
But what happens afterwards definitely does require skilled human involvement. Breech explains that the first step in the subsequent analysis process is a painstaking slice-by-slice visual inspection of CT data on a computer screen by one of the half-dozen individuals who have been trained to identify the tiny indicators of possible imperfections. Interestingly, he says that sheer visual acuity is their crucial capability and that the necessary engineering knowledge can be grafted on to that. One of them, in fact, is a typographer whose previous experience was in the printing industry. An operator can check about a hundred ‘slices’ every 15 minutes.
Nevertheless, further processing of raw CT data does take place. In this respect, Breech says that a particularly important tool is a software system called Volume Graphics that transforms the initially “flat” slices generated by the CT system into much richer 3D imagery. The purpose of this, he explains, is to support its use for metrology applications, achieved through direct comparison of the CT data with a reference CAD model of the part involved. Still, Breech says, the operator’s skill and experience are the key factors in enabling the data to be exploited to useful purpose. “You need to know what you are looking for and how to report it,” he explains, adding that though there is software to perform this task the company does not yet regard it as adequate for its demands.
Unsurprisingly, therefore, Edward Grainger takes the view that the company’s use of CT has been a “game changer”. But he is careful to stress that it has been so only in the context of the increased knowledge and competence it has helped create among the company’s workforce – it is not in any sense a technical quick-fix. The key thing is “the depth of understanding of castings” that the company now possesses. As he puts it: “If we see something that needs investigating we don’t stand around debating it, we say ‘come one let’s check it’.”
Following the company formula
Castings supplier Grainger & Worrall is based near Bridgnorth, a picturesque town just to the west of the one of the UK’s main automotive manufacturing hubs, Birmingham. The bulk of the workforce, 500 staff, is based in a set of brick buildings on an industrial estate on the hillside above the town. About 100 out of that total are what the firm’s managing director Edward Grainger would term “engineering” personnel, whether apprentices or post-graduates. “Skilled operatives” such as pattern makers would, he says, comprise the same number again. A further 100 staff are employed at a site a few miles from Bridgnorth, a machining and assembly operation at Telford.
The Bridgnorth site is the location not just for actual casting operations but also supporting design and development activities and some machining, as well as sales and administration. Altogether they constitute a business that now has a turnover of roughly £46m ($66m) a year derived from serving three distinct, if related, markets. These are, says Grainger, acting as a technology developer for the motorsport sector, providing prototyping services mainly (though not entirely) for the automotive sector and acting as a low volume producer (between 2,000-5,000 parts per year in each case) for a number of high-end carmakers. In the latter case, he mentions examples such as Bentley, McLaren, Aston Martin, Porsche and Bugatti.
Categorising the sources of the company’s income, Grainger’s observes that it is split roughly 50-50 between simply “selling castings” and other “value added” activities. Prototyping operations figure large in the second of those areas. Grainger says that the company carries out around 600 such “new product projects” every year. The formula certainly seems successful. It enabled the company to weather the downturn that hit the global economy in 2008 when turnover dropped to just £14m and since recover by maintaining a steady 10%-15% annual growth – during which time the workforce more than doubled. Grainger adds that the fact that the company does not have to worry about generating returns for external shareholders is a relevant factor. “We can take a longer term view of things,” he observes.
Source: Automotivemanufacturingsolutions.com
Related Posts
EV components: Surviving the valley of death with sand casting
When it comes to producing components for electric vehicles that are lighter (creating lighter,...
COMPANY OF THE YEAR 2018
We are pleased to confirm on Friday night Grainger & Worrall came home with the nights top award...
4 challenges of casting a giga cast component
Casting large components such as giga casting requires a complete shift in terms of approach; both...