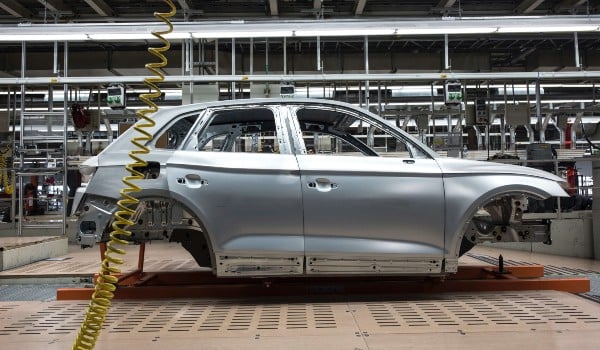
Lightweighting is a vital concept in current automobile manufacturing, and for good reason – there is an approximate 3-5% decrease in carbon emissions for every 220 pounds lost.
Weight reduction is unlocking the potential of electric vehicles in making them greener and more economical, which is becoming increasingly more important as we approach the 2030 ban on new petrol and diesel cars.
In this article, we cover the main aspects of EV lightweighting, including material substitution and reduction, fuel economy targets, large prototyping, and 3D printing, along with the challenges involved.
FUEL EFFICIENCY
The fundamental idea behind lightweighting is that a lighter vehicle needs less energy to move - a very appealing prospect to customers who expect their cars to be ever more fuel efficient. This demand is being met with the development of lightweight materials and cutting-edge manufacturing processes.
Lightweighting is enabling EVs to carry larger battery packs and electric motors by making other parts lighter, balancing out the load of these heavy power systems whilst also improving electric range.
tHE tUCANA pROJECT
Jaguar Land Rover is researching advanced lightweight composites to develop EVs with better range and performance. The work is part of their Tucana Project, a 4-year program that aims to reduce energy consumption and put an end to 4.5 million CO2 emissions between 2023 and 2032.
In the hope to accelerate EV adoption, Jaguar Land Rover will replace aluminium and steel with composites that reduce emissions and improve efficiency.
Their target is to make their vehicles 35 kilograms lighter, thereby allowing larger batteries to be fitted. Jaguar Land Rover aims to have manufactured prototypes of their Tucana test vehicles by 2022.
More For You:
Innovations in energy for transport
Electric vehicle metal innovation: it's not all about battery technology
What role will sand casting play in future transportation?
Alternative Materials
Traditional components, such as iron and steel, are being replaced with alternative metals and polymer composites. These materials can reduce the mass of a vehicle by 20-50%, increasing the range, lifespan, and performance of EVs.
polymers
Lightweight polymers and polyurethane composites are ideal for replacing glass and metal in window glazing and body panel components, as they are lighter than traditional materials and they retain their strength well.
An EV battery can increase the weight of a vehicle by 35%, so polymers are useful to minimise the mass of other parts. As a result, plastic composites are increasingly being used in the manufacturing process for shape optimisation and material substitution.
ALTERNATIVE METALS
-
Carbon fibre: it is lighter than steel and 10 times stronger, but more expensive than traditional metals.
It is expected to be used more in EV manufacturing, with Volvo already exploring its uses. After years of study, they are aiming to replace steel body panels with carbon fibre that could store power like batteries.
Not only would this reduce body mass, but their findings also indicate that body panels could charge an EV faster than traditional batteries.
-
High Strength Steels: vehicle heaviness can be reduced by replacing steel with high-strength steel. It is currently the dominant material used in light EVs as it is cost-effective and can be incorporated into the production process relatively easily.
-
Aluminium: the automotive market is the largest and fastest growing sector for aluminium producers. The metal can reduce the weight of a vehicle by 40% in comparison to using steel, making it an ideal lightweight compound for EVs. Its ability to lightweight can also reduce cost by getting rid of material unneeded in the casting.
Additionally, aluminium is recyclable, which is an appealing quality to the growing number of consumers who are prioritising sustainability.
-
Magnesium: it is the lightest structural metal, weighing about a quarter of steel and is 35% lighter than aluminium.
It is already used in car wheels, door panels, seat frames and inner door frames, but researchers are also looking into replacing the lithium in EV batteries with magnesium as it has a high volumetric energy density.
However, it is costly, with some reports suggesting that magnesium is 7 times more expensive than steel.
Large prototype castings
Large prototype castings are an effective way of reducing weight. Tesla is using a large structural die-cast aluminium piece for the underbody of their Model Y.
Their giga press has great lightweighting potential for EVs, offering 10% mass reduction, 14% range increase, and 370 fewer parts. In light of this, Grainger and Worrall have been working on prototype sand castings that replicate die-cast parts used in the Giga Press.
3D Printing
Additive manufacturing is widely embraced in the automotive industry and is a key lightweighting technique. Used in design, prototyping, and tooling, 3D printing offers the same performance as traditional parts but produces lighter substitutes.
It is another way that the load of EV battery packs can be offset. In December 2020, Porsche revealed that it had been using additive manufacturing for some of its electric vehicles, such as its Taycan model.
The outcome was a positive one: they found that prototype housings for electric drives were stronger and lighter.
Challenges
Weight reduction can create difficulties in EV manufacturing, repairing, and maintenance, as different processes must be altered for specific lightweighting requirements. As a result, automobile manufacturers are forced to make adjustments – some of which can be costly.
Lighter materials usually require more energy to produce and workers must be trained to work with lightweight materials. The consequence of this is that manufacturers are at risk of reducing the market by limiting lightweighting to just premium products.
Overview
Lightweighting offers many benefits for the future of electric vehicles, such as increased range, longevity, and performance.
Implementing it in mass production is the biggest challenge for lightweighting solutions, as manufacturing and maintenance procedures must be altered at a cost. However, labour can be eliminated with cutting edge technology such the Giga Press, which can make EV production easier and quicker.
It will help transportation become more energy efficient as it heads towards a zero-emission future. The future is electric, and lightweighting is helping us get there.
Want to find out more about how sand casting is supporting wider electric vehicle manufacturing? Read our ebook Making EV Components with Sand Casting by clicking on the button below.
Related Posts
Electric vehicle metal innovation: It's not all about battery technology
While much of the focus of materials used in electric vehicles remains on battery technology, metal...
4 Ways Sand Casting Supports Electric Vehicle Manufacturing
Achieving global aims of carbon-neutral transport is a huge challenge. Electric vehicles are set to...
Engine Castings: Thermal Efficiency & Innovation
The UK is banning all new petrol and diesel cars and vans from 2040, driving the need for smaller...