4 min read
Why Sand Choice Can Make or Break Precision Casting
By: Grainger & Worrall on Jul 16, 2025 11:35:27 AM
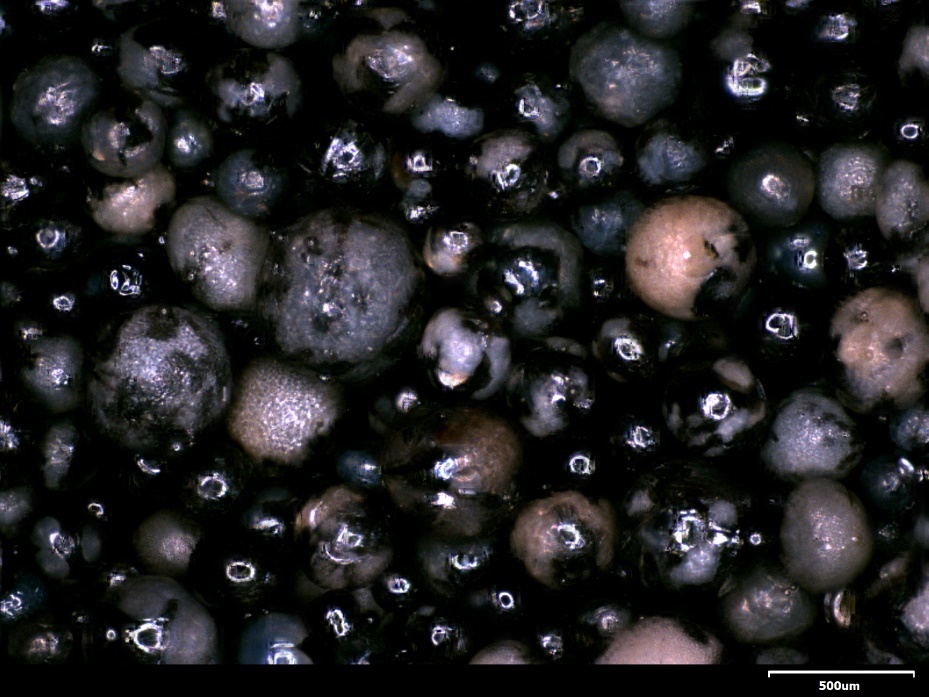
When it comes to sand casting, it’s easy to assume the material choice is simple.
In reality, sand selection is most often driven by mechanical performance, cost-efficiency and production requirements, especially as castings become more complex. While precision and surface quality are important, they are a part of a wider set of considerations when choosing the right sand for the job.
At Grainger & Worrall, we understand that casting accuracy begins at the grain level.
The properties of sand under thermal stress, its interaction with binders and its impact on defect formation all shape the outcome. This article explores the types of sand used in casting, their unique properties and why sand selection is key to precision sand casting.
Types of Sand Used in Casting – Silica, Zircon and Synthetic Sands
When it comes to casting, not all sands are created equal.
The type of sand you use can generate a completely different outcome, from how smooth the surface is to how well the casting meets dimensional tolerance and even the mechanical properties of the casting.
There are a few big players in the world of casting sand, and each brings something different to the table.
Silica is the most common, but zircon, other mineral-based and synthetic sands are often used when you need something stronger, more heat-resistant, or just more reliable for complex jobs.
So, how do we choose the right sand to give the best possible result?
Understanding Core Sand Casting Materials
Silica sand remains the most widely used sand casting material due to its low cost and wide availability. At Grainger & Worrall, it is central to many of our aluminium casting programmes.
However, it presents a key limitation: at 574°C, silica sand grades will transition from alpha quartz to beta quartz, causing linear expansion. This shift can result in dimensional inaccuracy, particularly in high-temperature castings such as steel or advanced aluminium alloys.
Zircon sand offers superior thermal stability and dimensional consistency. It also promotes better mechanical properties in the casting. Zircon also has the lowest thermal expansion of all stand types and neutral buoyancy in aluminium, making it the premium sand media for high-integrity sand casting, involving intricate core geometry.
Mineral sand, derived from supercooled bauxite, presents another option.
Its spherical grain structure aids compaction and flow, as well as performing well thermally. However, it cannot be efficiently reclaimed due to its impact on pH levels, making it less suitable where sand reclamation in casting is a priority, as initial reclamation is difficult.
Silica Sand Grades and Grain Size: Why Fineness Matters
Grain size directly impacts precision sand casting, with finer grains producing smoother surfaces, which are not only more aesthetically pleasing but also specified by customers.
However, as the grain number increases, the permeability drops. This demands more binder to maintain strength, which can lead to increased gas formation during pouring, which potentially creates defects unless carefully managed by experts.
Silica Sand Grades at Grainger & Worrall
Grainger & Worrall uses four main silica sand grades tailored to specific applications:
-
60 Grade – The primary grade (96–97% silica).
-
Fine silica – 99% purity, 97-micron average grain size.
-
Coarse 65 grade – Designed for use in 3D sand printers.
-
95 grade – A niche option for selected applications.
Each sand is selected based on a project’s needs for surface finish, permeability and binder compatibility.
How Sand Types and Binder Systems Impact Precision and Strength
The binder system is as critical as the sand itself. Our sand printing systems use a Furan binder, derived from vegetable matter, and a High-hot strength phenolic binder. These binder systems have good hot strength properties, which maintain dimensional stability.
To further optimise results, core coatings such as aluminosilicates are applied in some applications, notably in motorsport castings, to achieve ultra-smooth finishes and reduce porosity.
Testing and Quality Control in Precision Sand Casting
Grainger & Worrall deploys extensive quality control measures to ensure consistent casting results:
-
Sieve testing classifies grain distribution between 1,000–63 microns.
-
Loss on ignition testing quantifies binder content by burning sand at 900°C, helping prevent gas-related defects.
-
Gas CT and X-ray scans verify internal component integrity at the final stage.
-
pH testing monitors the acidity or alkalinity of the sand mix, ensuring it remains within the optimal range for binder reactivity and casting consistency.
-
Strength testing assesses the compressive and tensile strength of sand samples to verify mould stability during metal pouring.
Each step ensures the chosen sand casting materials meet the required standard across functionality and aesthetics. Discover how rigorous material analysis ensures reliability in casting outcomes.
Sand Reclamation: Driving Sustainability and Cost Efficiency
Sustainability is embedded in our operations. We reclaim up to 99.6% of our sand through mechanical and thermal processes, primarily for silica and zircon sands. Bauxite sand is not reused due to the effect of thermal reclamation on the pH of the sand.
This focus on sand reclamation is supported by simulation-led usage planning and advanced material testing, helping us balance environmental responsibility with the precision our clients expect.
Simulation software allows us to model sand use in advance, reduce waste and keep material costs low. This not only supports client budgets but also aligns with our environmental objectives. Learn More About Sustainable Sand Casting.
Choosing the Right Sand for Casting Accuracy
Selecting the right sand for casting is a system of trade-offs, optimisations and context-based adjustments. We carefully assess the project and its objectives and apply these trade-offs to decide on the right sand for the job.
We tailor each solution, whether it’s fine-grade silica sand for a superior finish, zircon for dimensional reliability, or hybrid blends for thermal stability. Every grain counts. With near-zero waste reclamation, simulation-driven efficiency and advanced material testing, we’re proving that performance and sustainability are not trade-offs; they’re the future of casting.
Related Posts
How does sand casting support giga casting prototypes?
Within the automotive industry, giga casting is a relatively recent technology. As a result, there...
How do you use sand casting to prototype a die-cast giga casting?
You might have noticed that IDRA’s Giga press is gaining increasing coverage regarding its...
EV components: Surviving the valley of death with sand casting
When it comes to producing components for electric vehicles that are lighter (creating lighter,...