3 min read
How can sand casting contribute to a carbon-neutral future?
By: Phil Ward on Apr 23, 2021 11:40:02 AM
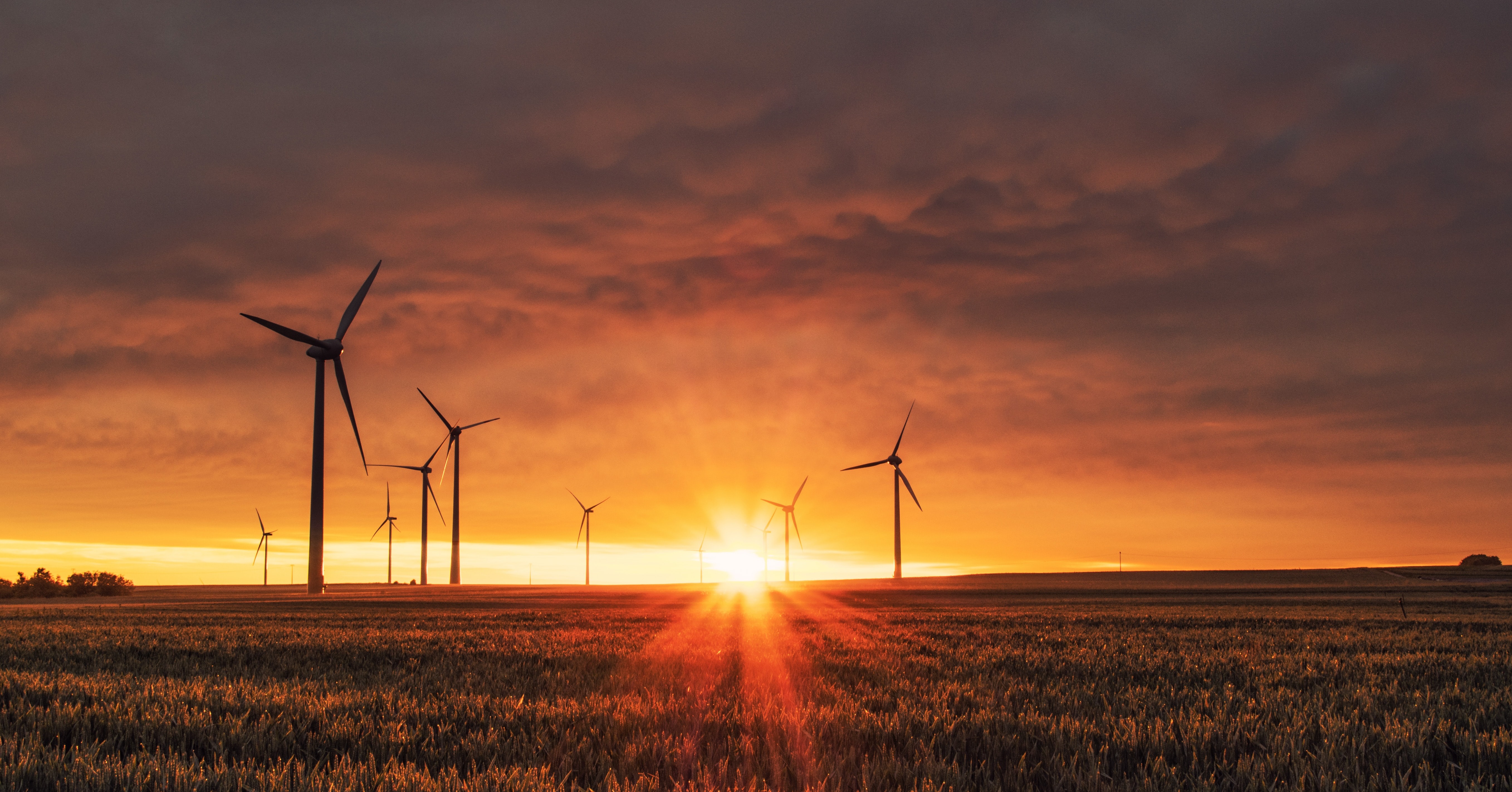
In 2021, manufacturing and production advances are being driven by the challenges of addressing climate change impact, achieving carbon-neutral aims and a circular economy, as well as global shifts in economics and technology capability.
It’s a potentially exciting, but also hugely challenging time for engineers and manufacturers. Any response to sustainability must also be balanced with commercial drivers of cost and performance; requiring innovation and optimisation across industries.
Complex castings are vital in this response, reducing fuel usage and material weight to reduce C02 emissions, particularly in automotive sectors. Engineers are innovating to make components with fewer parts and lightweighting existing components. The production processes themselves are also essential, with focus placed on circular processes that have high recyclability. Sand casting offers huge potential to achieve this.
Lightweighting and part count reduction
Global low emissions targets mean that innovation is needed in terms of design, functionality and performance of components. This is particularly true in automation (both in ICE and EV), where the lighter the vehicle (regardless of power source), the less energy is needed to make it move. This then allows weight of other components to be reduced, for example with brakes. Reducing weight reduces fuel usage, but it also allows EVs to have increased battery range, and this is essential for wider adoption.
Casting offers a huge opportunity to remove weight from a vehicle, both during prototyping and production to deliver lighter engines and structural components. Lightweighting potential is a particular strength of sand casting, where the ability to create shapes with complex geometries (due to core placement) in one single net part reduces part count and weight with reduced material usage.
recyclability of materials used in sand casting
The choice of alloy used in casting will determine the casting quality and material properties of the part, as well as the design functionality. Specially created alloys offer high performance combined with cost efficiency. Alloy selection impacts material properties such as corrosion resistance, weight, thermal conductivity and hardness.
Sand casting using aluminium alloys can reduce the weight of castings by using lower wall thickness, in turn reducing carbon emissions. Alloys with different compositions can be created, achieving specified material properties for each part. Material analysis and simulation using Magma can be used to predict alloy behaviour and refine the process; and this is especially valuable in prototyping.
As well as the potential to support carbon-neutral goals with complex, lightweight castings, the sand casting process itself is environmentally friendly. Sand casting is an essentially circular production process where 99% of materials can be recycled. When ‘out of the ground’, aluminium is extremely recyclable, important for environmental concerns, but also for whole-life cost analysis.
Driving future shaped innovation with prototyping
As we globally push boundaries in technology, performance expectation and sustainability, prototyping becomes more and more essential. The relative speed, low cost and flexibility of the sand casting method adds huge value as a prototyping method.
The prototyping process is now the ideal arena for detailed characterisation of materials and products. When combined with powerful simulation software, prototype properties can be fine tuned to meet functional requirements without over engineering, reducing unnecessary material and weight.
Technological advances of sand casting
Modern sand casting utilises technology to optimise the process, in design, production and testing.
CAD software allows virtual engineering and design, where 3D sand printing can produce sand cores in a matter of hours, significantly speeding up the process. Simulation software such as Magma allows predictability of material behaviour. This is vital when maximising engines or components to be smaller or lighter.
Testing capability is also enhanced with methods such as CT scanning, improving the verification process.
To wrap up
Sand casting is well placed to support aims of a carbon-neutral future. As well as being an inherently recyclable process due to the sand and aluminium used, the ability to create shapes with complex geometries and high material properties contributes to lightweighting and part count reduction for reducing C02 emissions.
To find out more about what can be achieved with the sand casting process, we've put together a free, downloadable eBook The Basics of the Sand Casting Process.
Related Posts
How do you use sand casting to prototype a die-cast giga casting?
You might have noticed that IDRA’s Giga press is gaining increasing coverage regarding its...
Why Sand Choice Can Make or Break Precision Casting
4 challenges of casting a giga cast component
Casting large components such as giga casting requires a complete shift in terms of approach; both...